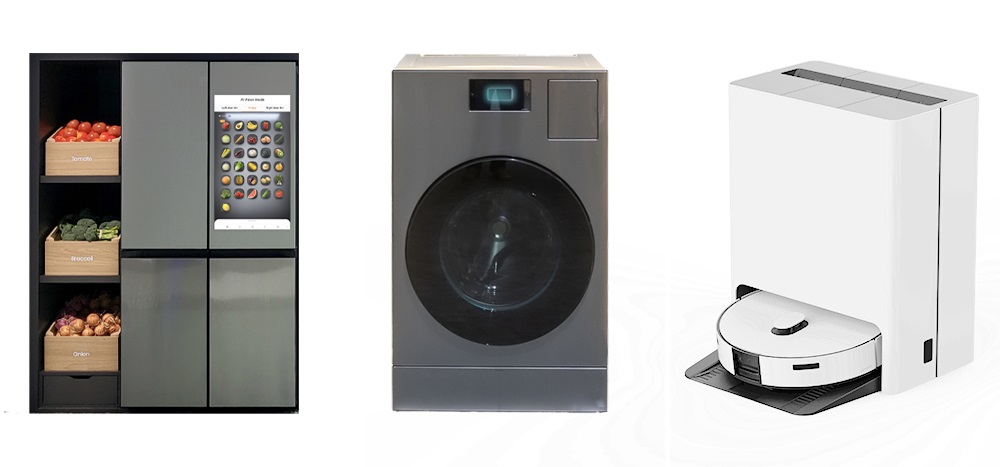
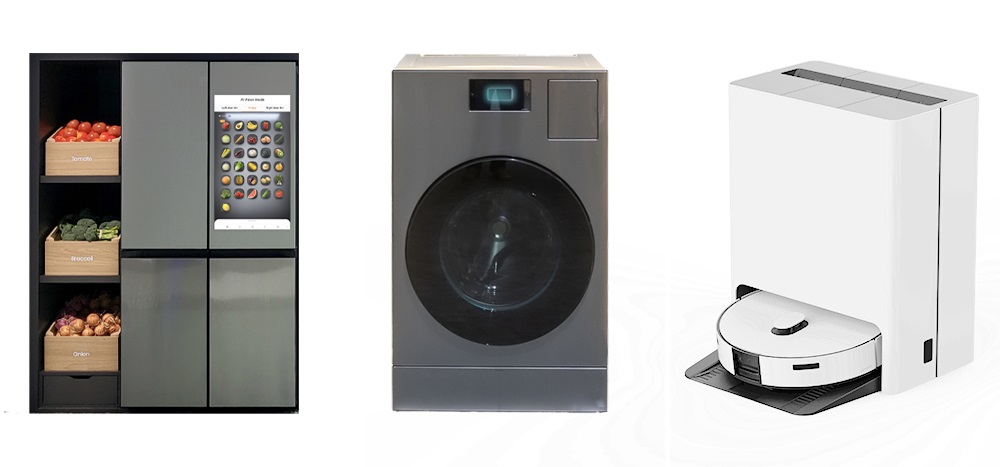
Common Sub-Zero Refrigerator Issues and Repair Tips From Professional Tech
Kitchen appliances, Sub-Zero refrigerator stands as a symbol of quality, elegance and functionality. Renowned for its cutting-edge refrigeration solutions, Sub-Zero refrigerators are the epitome of luxury, ensuring optimal preservation of food and beverages, but even these high-end units may encounter occasional malfunctions, prompting the need for professional repair services. In San Diego CA residents turn to the professionals at Premier Appliance Repair, located at 7919 Silverton Ave. in San Diego for same day Sub-Zero, Wolf service. https://subzerorepairsandiego.com/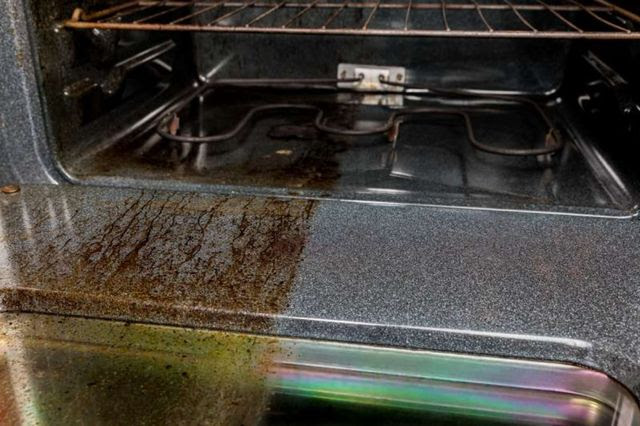
What Is the Oven Self Clean Feature?
The self-clean oven feature is a convenient function found in many modern ovens, designed to ease the task of cleaning. Premier Appliance Repair techs find using self cleaning option on older units, improperly installed wall ovens that have poor air circulation, no maintenance performed could be a big problem and costly repairs. If you experience problem after using this option contact us-We are here to help.www.premierappliancesandiego.com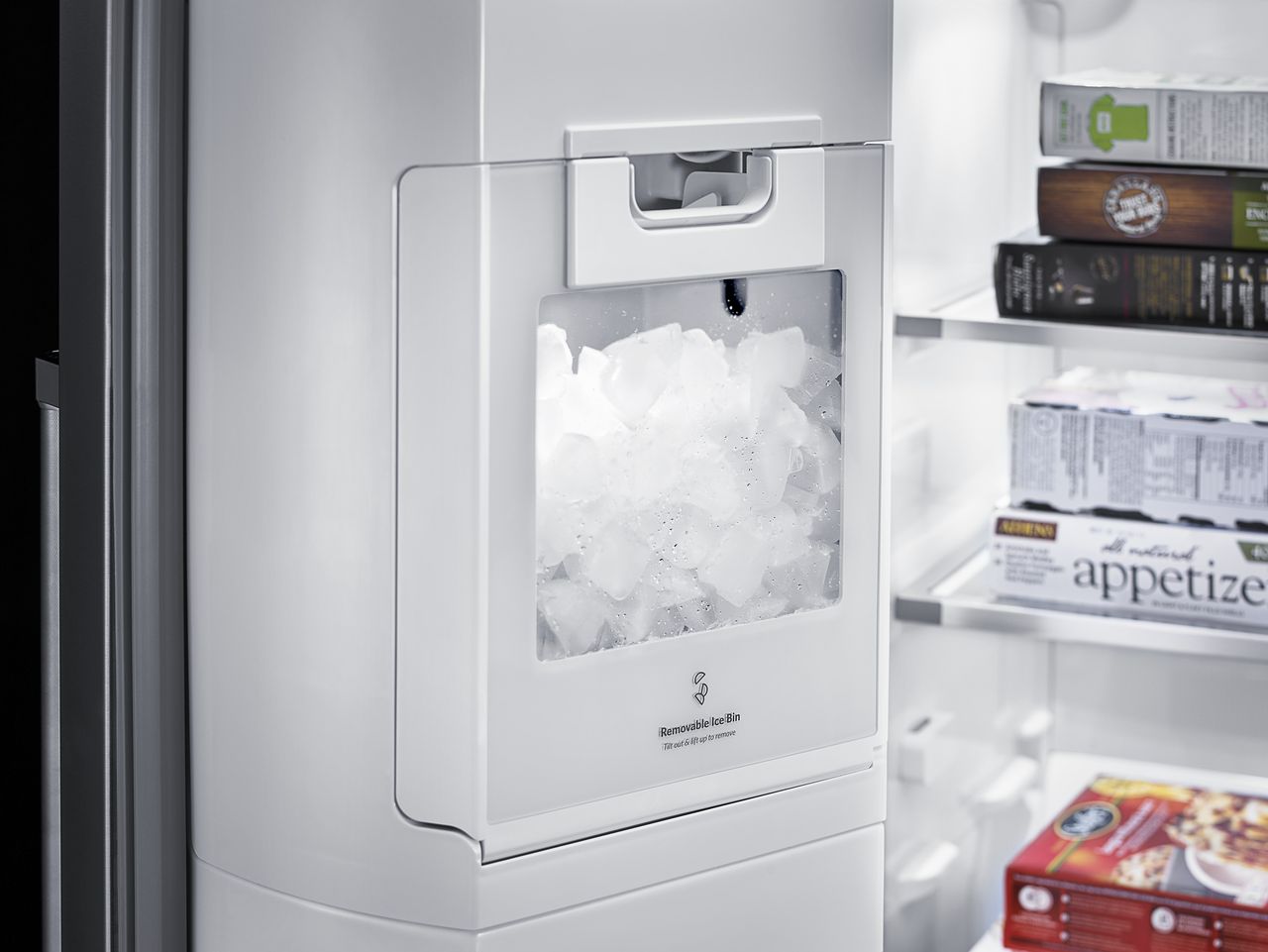
Is Your Ice Maker Overflowing? This May Be The Reason….
If you’ve been having problems with your ice maker overflowing, you may be wondering what’s going on. There are several reasons why this might be happening, and in this blog post, we will discuss some of the most common ones. We’ll also provide tips on how to fix the issue and keep your ice maker running smoothly!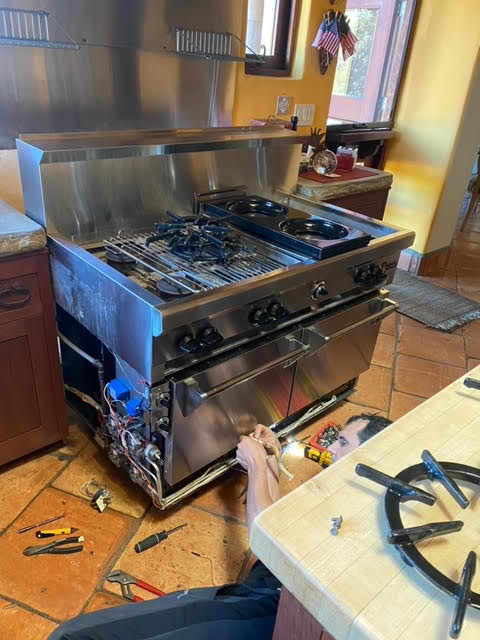
Ensuring a Smooth Escrow: How Premier Appliance Perfects the Home Inspection Process in San Diego
A home inspection is a critical part of the escrow process in San Diego and in California. It provides buyers with important information about the home's structure and working systems, whether the appliances in the kitchen and laundry room are fully operational or need some attention. This is where Premier Appliance Repair Service does it’s magic!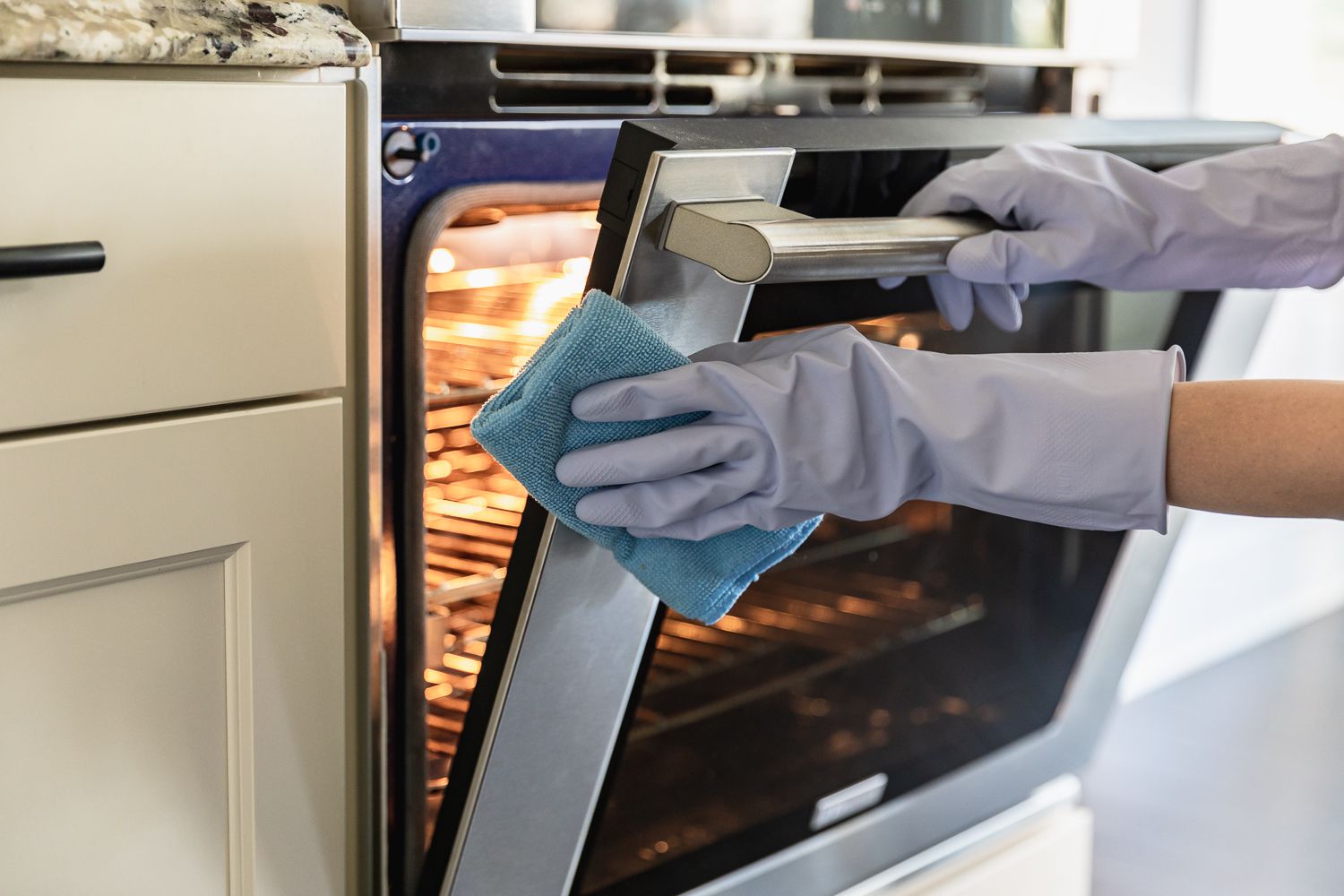
Oven door cleaning
Every home chef knows the annoyance of peering through a smudged oven door, trying to gauge if their culinary creation is baked to perfection. Those pesky stains, splatters, and spots can cloud the vision. Fear not! We’ve compiled a detailed list of oven door cleaning hacks to ensure a clear view and an even clearer mind. Contact Premier Appliance Repair at 619-377-6388 or visit: https://premierappliancesandiego.com/ Delving Deep into Oven Door Cleaning Hacks You’ve probably pondered, “How do you clean a really dirty oven door?” or “Why do these stubborn marks keep appearing?” To tackle these troubles, we’re breaking down each section of the oven door, discussing the culprits of dirt, and providing solutions for a pristine shine.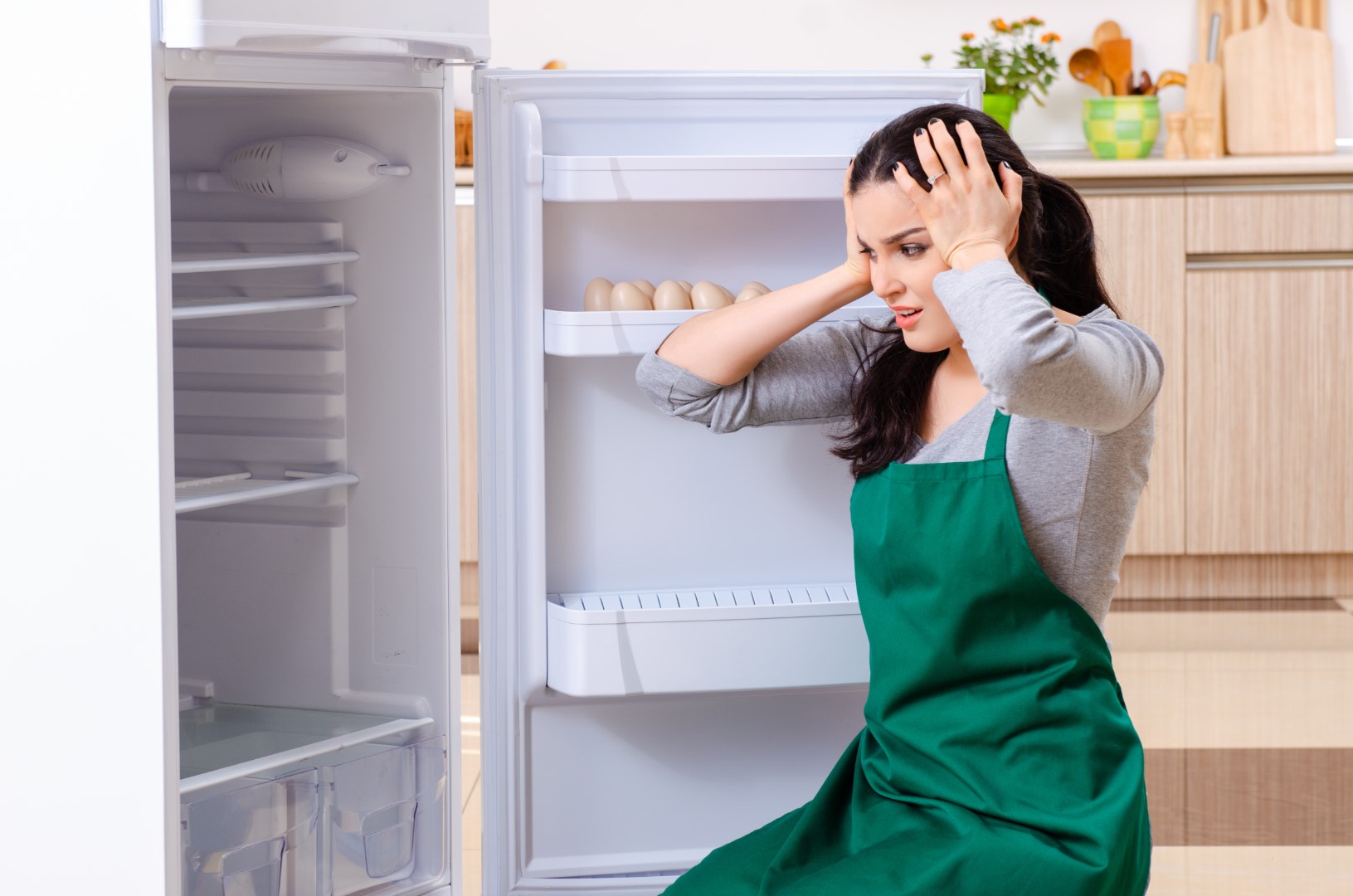
GE Freezer is Cold, but Refrigerator is Not? This May Be Why…
GE refrigerators are a popular choice in San Diego for many homeowners. Based on our in-house statistics we find the information to be accurate. Premier Appliance Repair in San Diego has trained GE technicians with lowest possible prices on parts due to the volume that we do with our GE parts vendors.GE refrigerator come in a variety of styles and sizes and can be used to store both food and drinks. GE refrigerators are reliable machines, but sometimes they may develop problems. One common problem homeowners experience is that a GE freezer is cold, but refrigerator is not.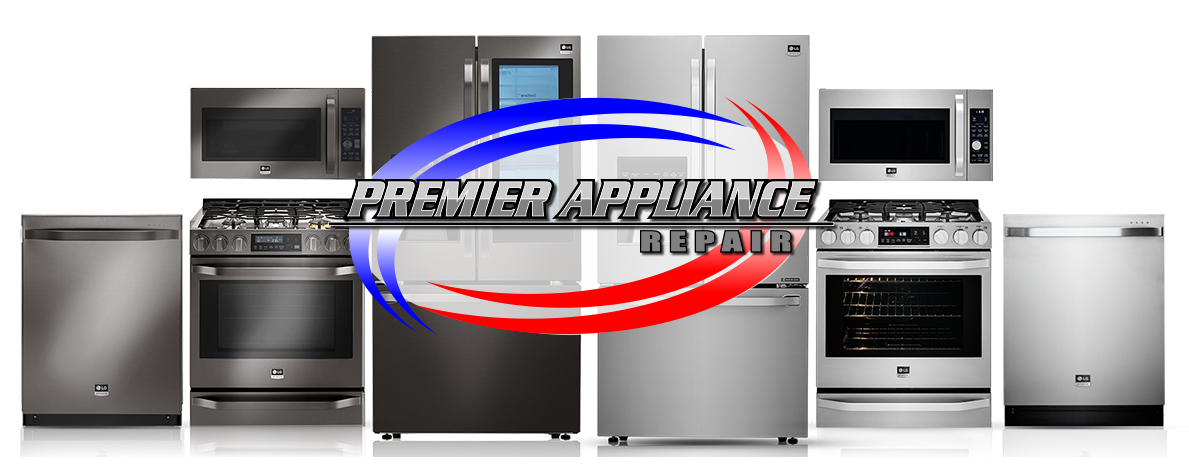
Premier Appliance Repair. What we do?
Our extensive knowledge and experience of all major brands will help to resolve and repair your appliances the way it should be repaired. Our techs know your appliance!!!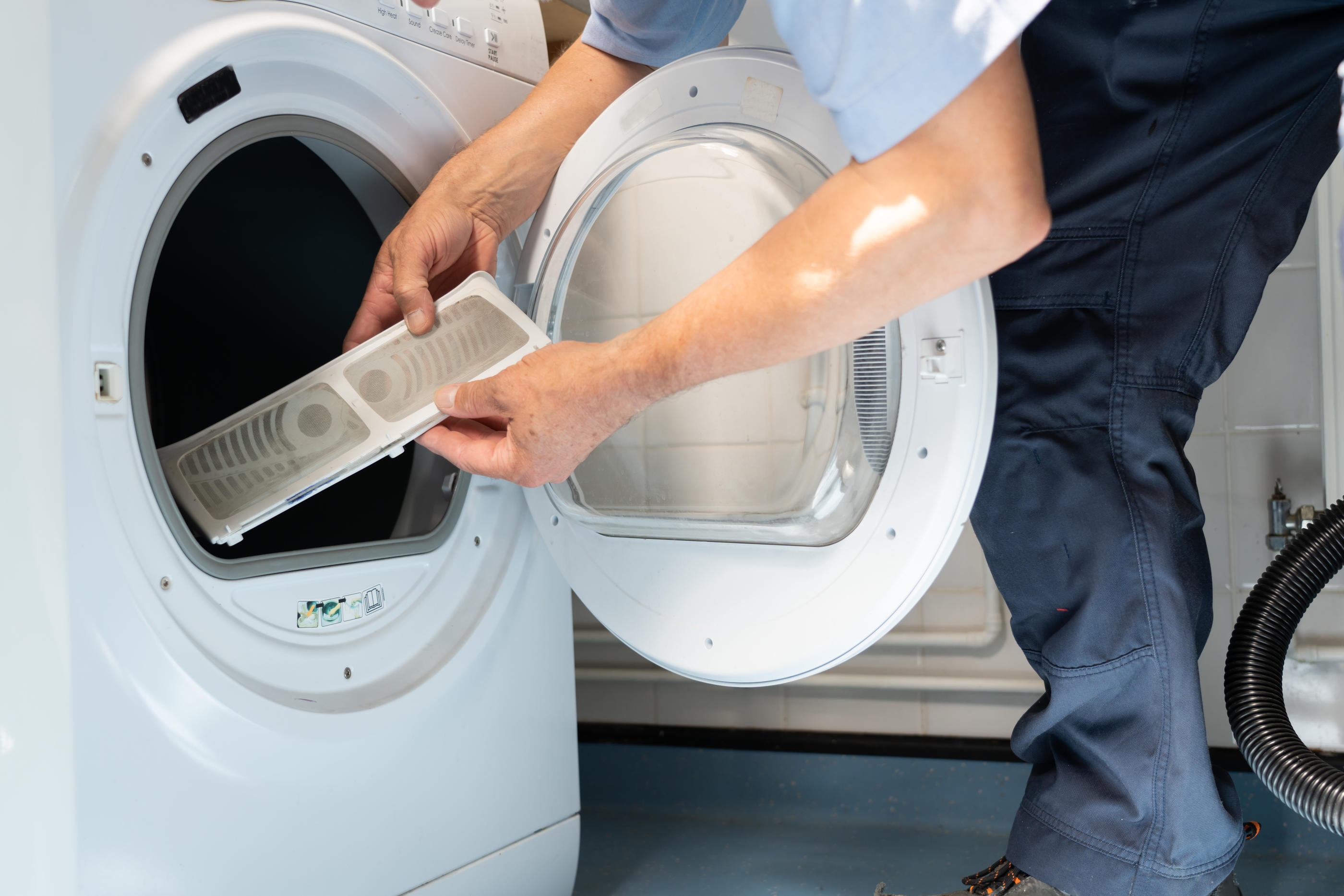
Dryer Maintenance Tips in 8 Easy Steps
Keeping dryer vents clean not only improves performance but increases efficiency and reduces the risk of dangerous dryer fires. How do you clean a dryer vent? After disconnecting the vent from the wall and dryer, use an appliance brush and vacuum hose attachment to remove accumulated lint. Our step-by-step guide details how to clean a dryer vent to keep this trusty appliance running safely and smoothly. Call your local experts at Premier Appliance to do professional work for you on your dryer or washer or any other appliances.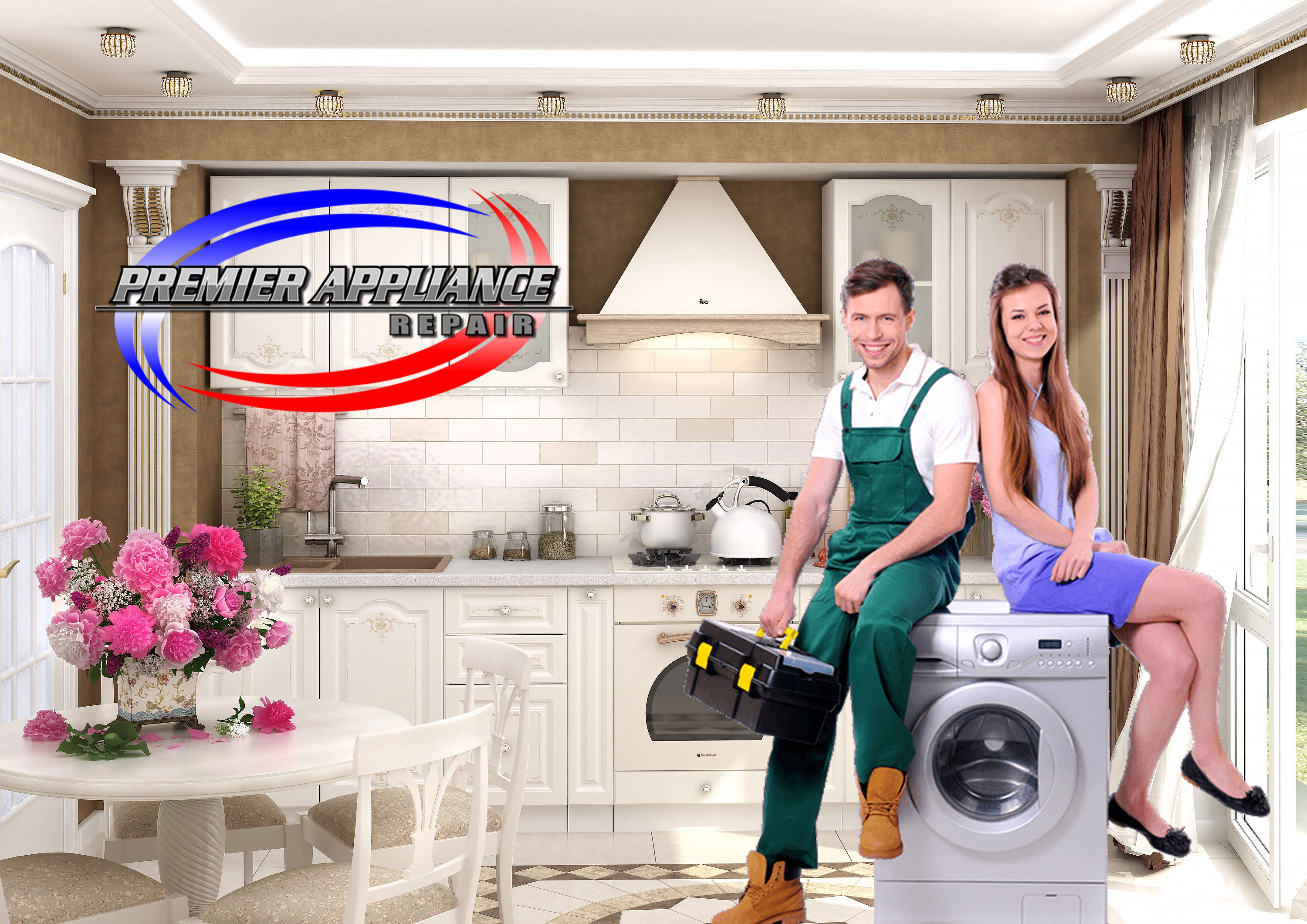
Should You Repair or Replace Your Washing Machine?
Deciding whether to repair or replace your washing machine can be a tough call. But it’s also an important one, as a washing machine is an expensive home appliance that serves a vital household function — and it can be quite inconvenient when it fails. Sometimes, washing machine repair is the cheapest option, while other times a replacement is more economical in the long run. Here are some factors to consider as you weigh your options for replacing or repairing your malfunctioning washing machine:- APPLIANCE REPAIR BONITA, CA
- APPLIANCE REPAIR NATIONAL CITY, CA
- APPLIANCE REPAIR SPRING VALLEY, CA
- APPLIANCE REPAIR DEL MAR, CA
- APPLIANCE REPAIR EL CAJON, CA
- APPLIANCE REPAIR ENCINITAS, CA
- APPLIANCE REPAIR LA JOLLA, CA
- APPLIANCE REPAIR LAKESIDE, CA
- APPLIANCE REPAIR POWAY, CA
- APPLIANCE REPAIR RANCHO SANTA FE, CA
- APPLIANCE REPAIR SAN LUIS REY, CA
- SAN DIEGO APPLIANCE REPAIR
- APPLIANCE REPAIR SANTEE,CA
- APPLIANCE REPAIR SOLANA BEACH, CA
- APPLIANCE REPAIR HILLCREST, CA
- APPLIANCE REPAIR POINT LOMA, CA
- APPLIANCE REPAIR OCEAN BEACH, CA
- APPLIANCE REPAIR MISSION VALLEY, CA
- APPLIANCE REPAIR PACIFIC BEACH, CA
- APPLIANCE REPAIR BAY PARK, CA
- APPLIANCE REPAIR LINDA VISTA, CA
- APPLIANCE REPAIR LOGAN HEIGHTS, CA
- APPLIANCE REPAIR NORTH PARK, CA
- APPLIANCE REPAIR SAN DIEGO
- APPLIANCE REPAIR NORMAL HEIGHTS, CA
- APPLIANCE REPAIR CLAIREMONT MESA, CA
- APPLIANCE REPAIR CARLSBAD, CA
- APPLIANCE REPAIR CORONADO, CA
- APPLIANCE REPAIR DEL CERRO, CA
- APPLIANCE REPAIR SORRENTO VALLEY, CA
- APPLIANCE REPAIR UNIVERSITY CITY, CA
- APPLIANCE REPAIR KEARNEY MESA, CA
- APPLIANCE REPAIR TIERRASANTA, CA
- APPLIANCE REPAIR MIRA MESA, CA
- APPLIANCE REPAIR RANCHO BERNARDO, CA
- APPLIANCE REPAIR RANCHO PENASQUITOS, CA
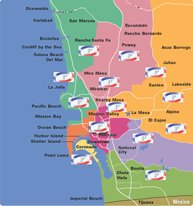
7919 Silverton Ave, San Diego, CA 92126